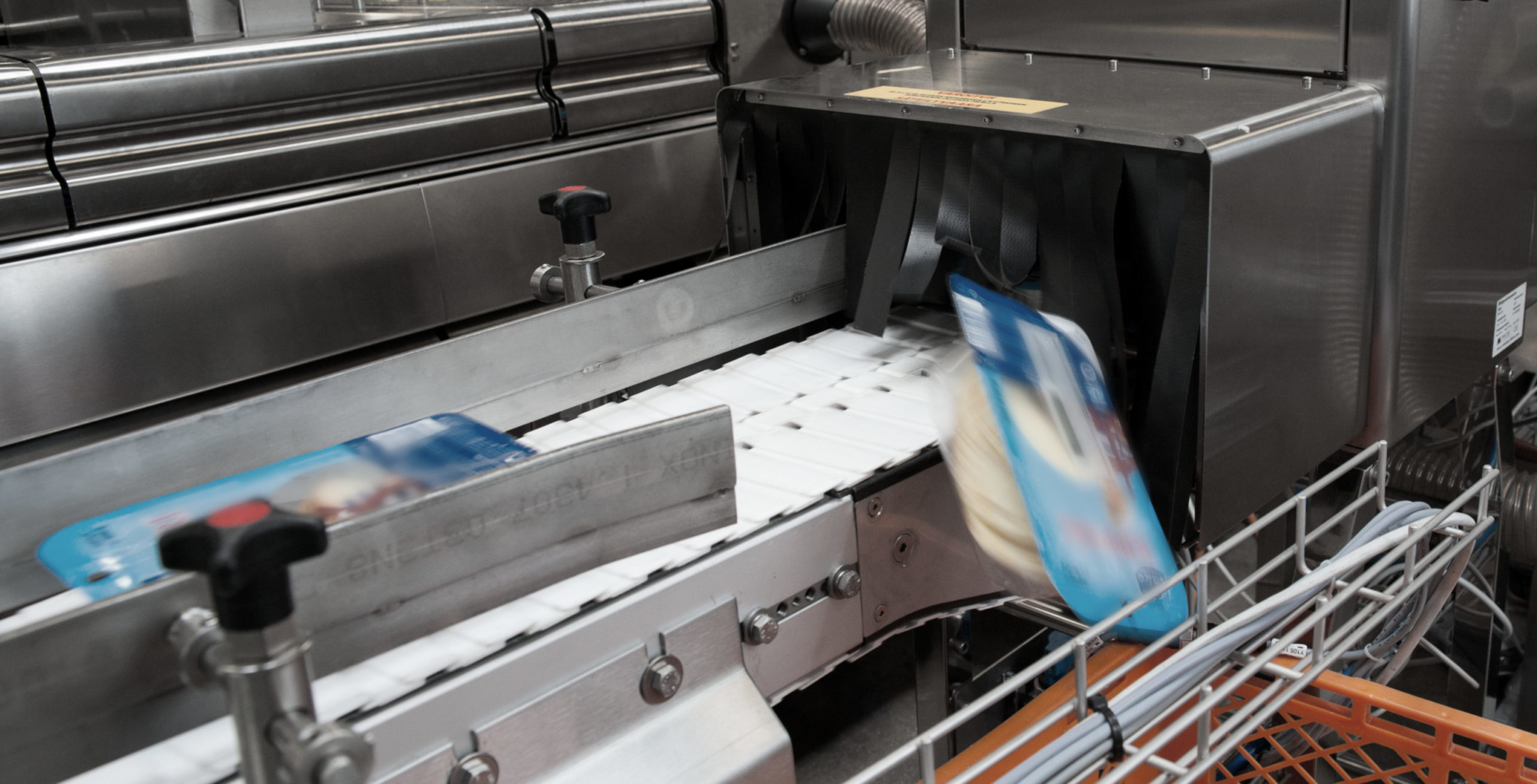
Amp Up Your
X-Ray Inspection System
with Integrated Add-Ons
Amp Up Your X-ray Inspection System with Integrated Add-Ons
As we know X-ray technology is a great way to inspect food products for any hazardous physical contaminations or unpleasant quality defects. Equipping the quality control system with industry/application-specific add-ons, food producers can further increase the system’s performance and operational efficiency.
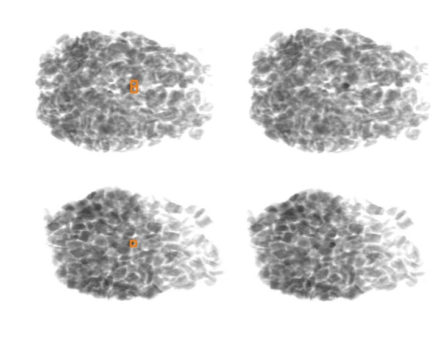
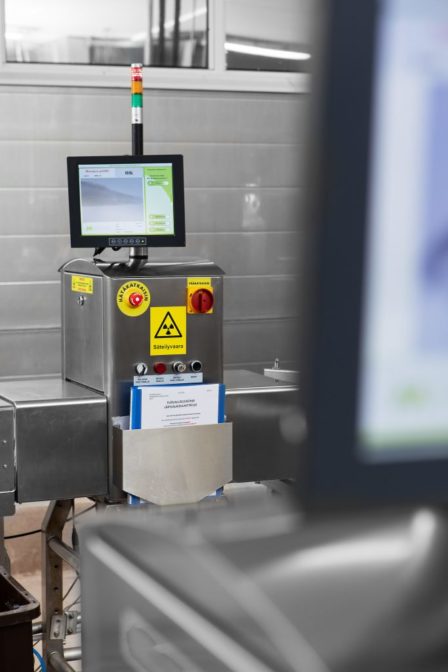
Complete Your X-ray System with Rejection
Implementing an X-ray to your food production line surely gives you the best inspection available for the food products and detects if there are any safety risks or quality defects. However, inspection alone doesn’t ensure that the non-conforming products are automatically removed from the production.
This is why every inspection system should be installed with a rejection unit. The combination of X-ray inspection and rejection makes a full quality control system or a Critical Control Point.
The rejection unit includes the rejecter itself (e.g. a pusher or an air blast) and a lockable rejection bin where the non-conforming products will be collected.
Rejection units have become a natural part of a complete Critical Control Point since they increase production automation, ensure total food quality control and minimize the possibility for human error.
The new trend in food safety is to implement a self-monitoring Critical Control Point. With the help of sensors, this system automatically alerts the operator staff if the rejection wasn’t successful, the rejection bin is too full, or the bin door is left open for a too long period of time. The system is simultaneously counting the products going in and out of the system to keep track of rejects, also monitoring that the air pressure is sufficient for the rejecter to operate reliably even if there are multiple consecutive rejects.
All of this can be included in your X-ray system by integrating the reject confirmation add-on, or by choosing MEKI ONE for your production lines since these systems are equipped with reject confirmations as a standard.
Add-Ons that Ease the Production Flow
To ensure the best possible detection, food producers should pay attention to the way the products arrive from the transferring conveyor to the X-ray. Add-on product guides help to line up the incoming products so that they arrive at the X-ray in a consistent way, preferably to the center of the imaging area supporting the best performance.
Also, with sensitive production flow, roller bridges can be utilized between the existing conveyor and X-ray system’s conveyor to close any gaps and further increase the smooth production flow.
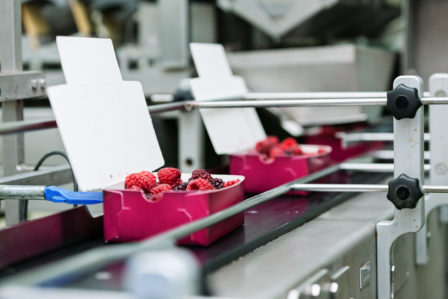
Better Performance in Challenging Production Environments
Challenging production environment is not a problem for an X-ray system, but food producers should acknowledge the product characteristics and the production environment when implementing an X-ray system. Industries, such as dairy or meat may require a higher IP class for their production equipment, and this is something that should be considered before the implementation.
Also, by using necessary add-ons, such as an integrated air conditioner, food producers can help to extend the system’s lifetime, reduce maintenance costs, and enhance the performance by providing an optimal inspection environment.
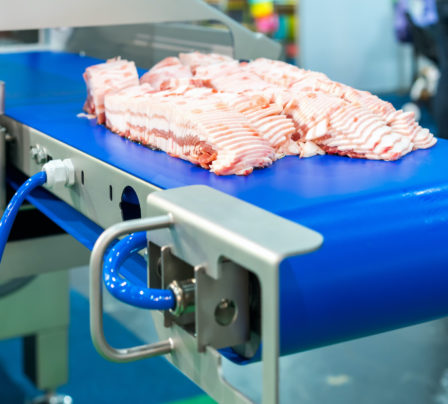
Additional Parts
In the food industry, there can be very specific requirements for the production line equipment. It’s good to take these requirements into consideration also when implementing the X-ray system, e.g. equipping the inspection system with a blue conveyor belt that is sometimes preferred in production where the product is still unpacked, e.g. meat production.
Sometimes the product’s characteristics such as very light weight, may require special attention when choosing the right consumable parts for the X-ray system. For example, these very lightweight products can have difficulties with product flow through the X-ray if using normal lead curtains. The curtains might slow down or turn the products, or in worst cases, the products might get stuck inside the system.
For these types of applications, it’s important to use necessary measures to ensure trouble-free production. A high-friction conveyor belt, light lead curtain materials and protective curtains in front of the lead curtains to reduce the friction are just a few options that can help when dealing with light-weight products.
To have the best possible inspection setup for your product, Mekitec recommends Application Tests where we make sure that the production flow, rejection, and foreign object detection are optimal and work flawlessly.