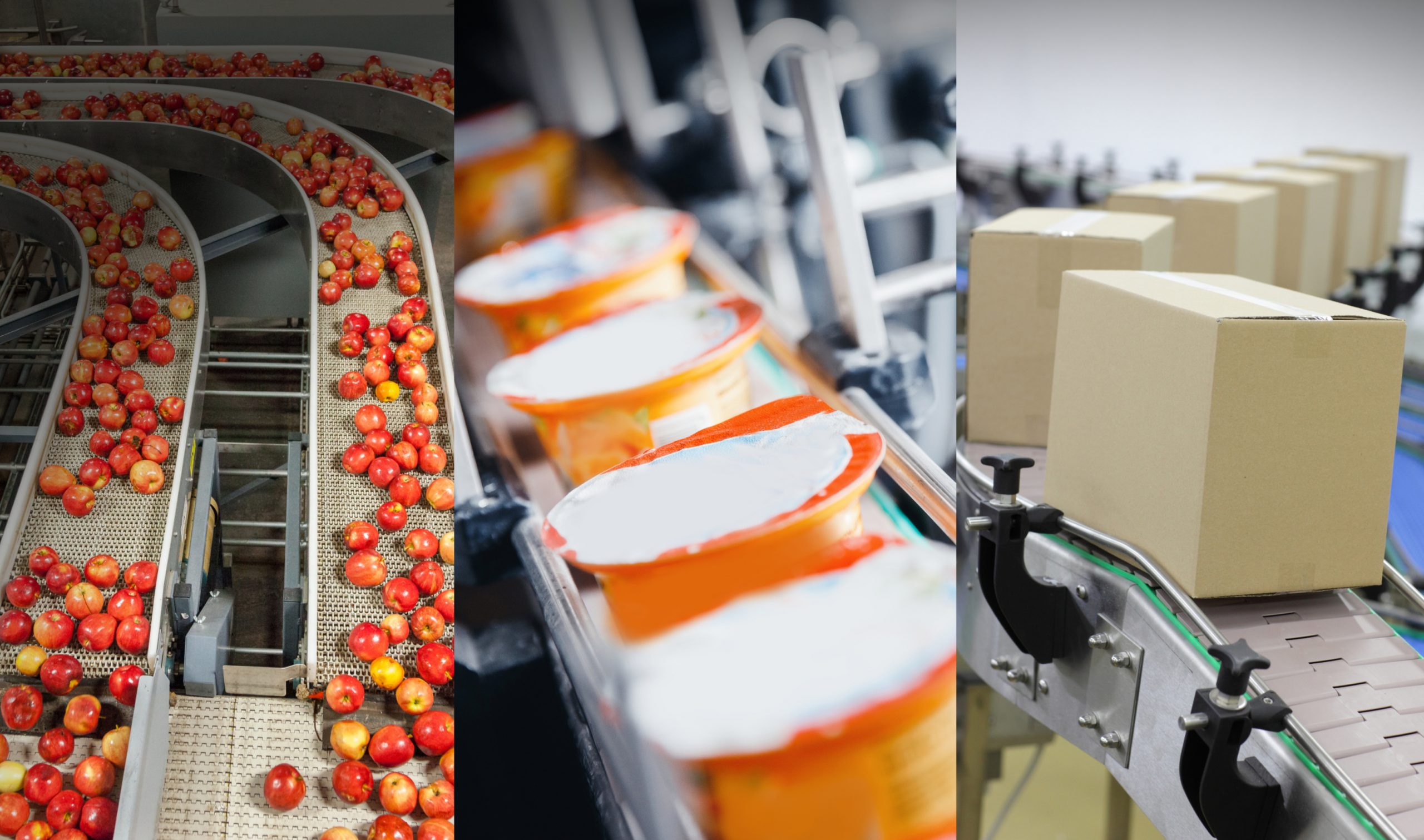
The main differences
between bulk, primary
and secondary
packaging inspection
Where to Place Your Critical Control Point?
Are you planning to implement new Critical Control Points to your food production, but struggle to decide at which stage of the production you should place the inspection system (bulk/unpacked, primary packaging, or secondary packaging)?
Each of these production stages has its own requirements and the most suitable inspection solutions.
In this blog, we will break down each stage and lay out the pros and cons of different inspection solutions.
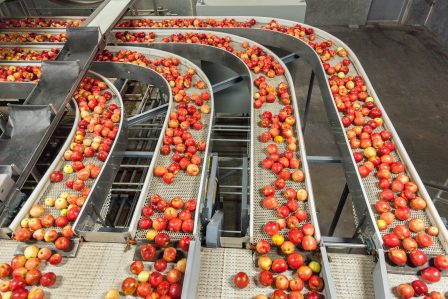
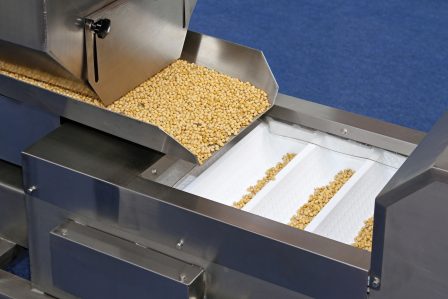
Why is bulk product inspection important but not enough?
Inspecting unpacked or free product flow, also known as bulk production, is important in order to verify the safety and quality of incoming raw materials. In this stage, food manufacturers often rely on different kinds of sorters, such as filters, lasers, or magnets.
This type of equipment helps them to mitigate the risk and sort out large foreign contaminants from the production process, but the equipment doesn’t set any alarms that would notify when a contaminant is found.
Sometimes, food manufacturers wish to implement inspection systems, such as metal detectors, X-ray inspection systems, or vision systems to inspect bulk production. However, this production stage can be very demanding for the inspection system and limit suitable solutions.
For example, inspecting unpacked products may require high washability and IP rating from the inspection equipment. This is why simple a metal detector might be a good choice for bulk production inspection. However, the technology itself has difficulties with certain product characteristics (also known as product effect) and has limitations in e.g., foreign object detection capabilities.
Also, it is very important to notice that even though the raw material is properly inspected and cleared from foreign contaminants, it doesn’t fully guarantee the safety of the finished products since they might be exposed to other contamination risks during the production process.
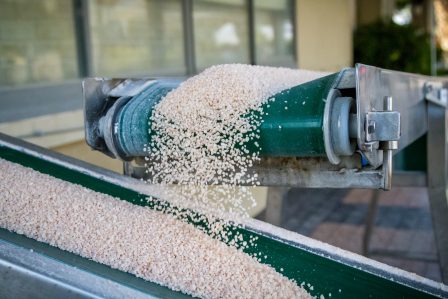
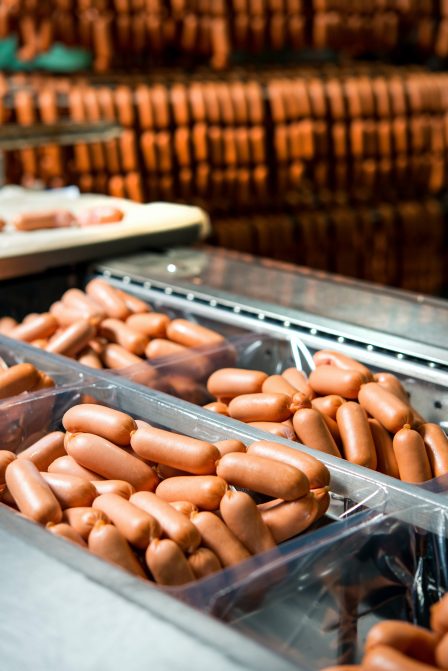
How primary packaging inspection provides the most accurate detection?
After raw material handling and processing, the food products move to the packaging stage. This is an ideal stage also for food safety and quality inspection since the product cannot be introduced to new contaminants after it is packaged and sealed.
In the primary packaging stage, food manufacturers have many inspection solutions to choose from, such as X-ray systems, metal detectors, and vision systems. All of which have their advantages as well as some limitations when focusing only on the product safety inspection.
For example, metal detectors cannot pick up non-metallic foreign bodies, vision systems only spot visible contaminants from the product’s surface, and X-ray systems cannot detect organic materials, such as insects and hairs, that are very light in terms of material density.
When comparing the three different inspection methods mentioned above, it can be easily concluded that using X-ray technology provides the most advantages to food manufacturers. With X-ray inspection systems they can:
- See inside the product without damaging it or the packaging (non-destructive inspection)
- Detect various hazardous foreign materials (e.g., metals, glass, and stones) and quality defects such as missing/broken pieces of products
- Automatically remove non-conforming products from the production line
- Get notified by alarm and visual cues if a contaminant is found
- Achieve full traceability and create a complete audit trail of their production
- Comply with any food safety standards or supermarket specifications
In the primary packaging stage, food manufacturers will also benefit from the most accurate detection rates for foreign contaminants. This is due to the fact that in a single food package, there is much fewer density variations or product effect than there is in secondary packaging.
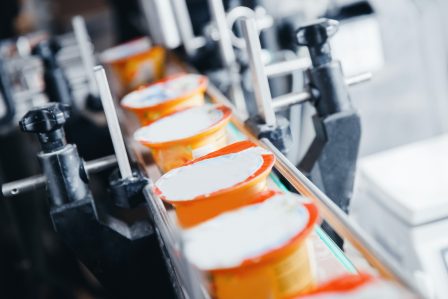
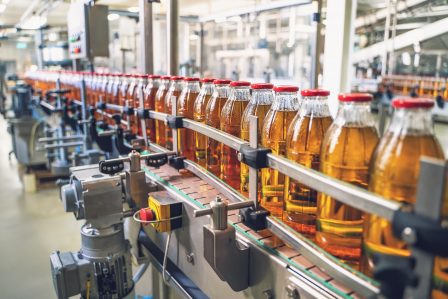
Also, inspecting primary packaged food with X-ray technology enables the detection of unwanted quality defects such as broken or missing products. This will ensure that food manufacturers deliver only high-quality products to their customers and eventually to consumers.
And at this stage of the production, food manufacturers can utilize the X-ray system as a traceability point to track and verify that each product was high-quality and free from contaminants when left from the packaging facility.
Read more about the 7 reasons why choose primary packaging inspection.
What are the issues with secondary packaging inspection?
After primary packaging, the food products are often placed in larger packaging, with two or more of the same products inside, called secondary packaging. In the eyes of inspection, this means there are more products and packaging to be inspected which obviously affects the detection rates with any inspection equipment; it adds up the product effect which can affect metal detector’s performance, as well as the overall density of the inspected products which makes it harder for X-ray systems to detect small contaminants.
Additionally, in the secondary packaging stage food manufacturers cannot utilize quality assurance functions that X-ray inspection offers. This would be a huge waste of the technology and its benefits.
Another notable downside is the size of the secondary packaging inspection equipment, as they need to have large enough openings to fit in even the most sizeable carton boxes. This also means that the system needs to have more powerful parts (e.g., the X-ray generator) which tend to be more expensive in terms of initial investment cost as well as the maintenance costs.
All in all, it can be said that secondary packaging is not the most efficient way to do food quality control.
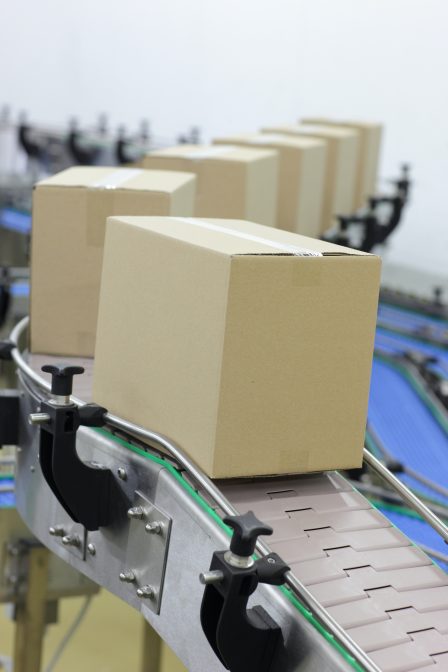
Application Test Here
Which inspection method to choose?
If you are still unsure which inspection method or solution would fit your operational needs, we are here to help!
Mekitec offers free-of-charge X-ray application testing, where we test your product samples with our primary packaging X-ray inspection systems and provide you a thorough report of the detection rates and overall performance that our systems can deliver.
After reviewing the report, you can make an educated decision on whether X-ray inspection technology would bring additional value to your food quality control.
