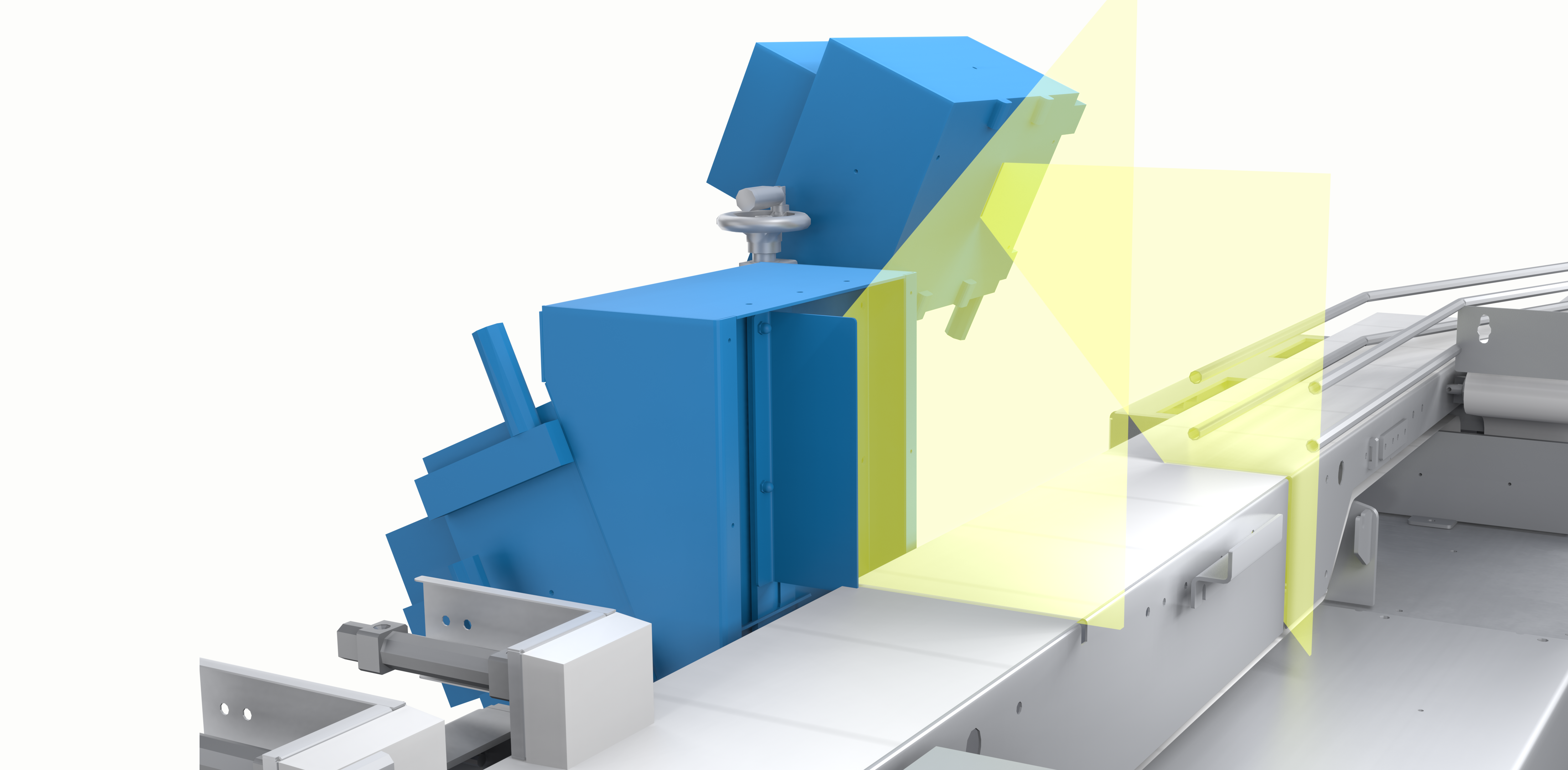
How X-ray
beam orientation
affects the inspection?
VERTICAL BEAM VERSUS HORIZONTAL BEAM SYSTEMS
Selecting the right X-ray beam orientation for your food products is crucial. There are three types of X-ray systems: vertical beam, horizontal beam (also known as side-shoot), and systems that are a combination of the two.
In this blog, we will explain the differences between these X-ray beam types and help you understand which one of them is the best fitting for your own food inspection needs. A good rule of thumb is that if your product is taller than wider, it should be imaged from the side to get a comprehensive view of the product. For products that are wide and low in height, the inspection should be done with X-ray systems where the beam comes from the above.
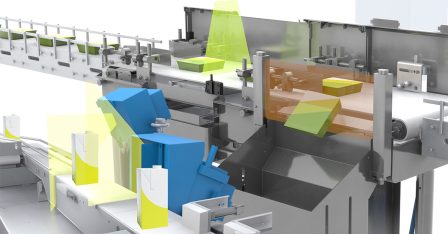
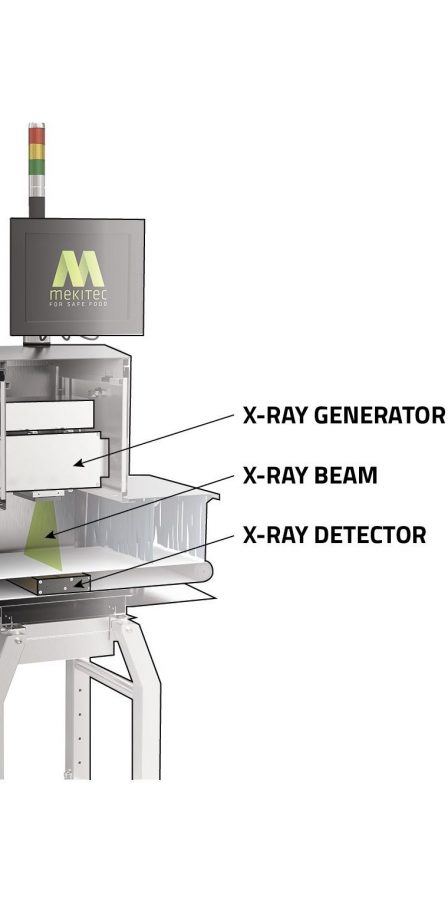
WHEN TO CHOOSE VERTICAL BEAM SYSTEMS?
Standard X-ray inspection systems are designed for inspecting flat packages like flow wraps, pouches, or small bags. In these systems, the X-ray beam is directed vertically, from the top of the product to the bottom (or vice versa).
Fast-moving consumer-packed food products are usually smaller in height than they are in width or length so inspecting them through the vertical cross-section where there is the least product to measure, provides the best sensitivity.
In vertical beam systems the basic X-ray imaging parts, X-ray generator and detector, can be placed in two different order. If the generator is on top of the inspected products, the system is called top-down and if the generator is below the products, the system is a so-called down-top X-ray system.
There are several benefits that you get from a top-down inspection system. The smaller distance between the generator and the detector enables a smaller generator size and requires less X-ray power, which prolongs the generator lifetime and reduces operating costs. The smaller sized generator also enables a compact size for the whole inspection system, which saves valuable production line space.
In the video below, you can see a vertical top-down X-ray inspection system (MEKI™ ONE) in action.
WHEN TO CHOOSE HORIZONTAL BEAM SYSTEMS?
Horizontal systems are primarily used for packaged food products that are taller than they are wide. In a horizontal (side-shoot) X-ray inspection system, the generator is at the front or rear of the machine, shooting a horizontal beam through the products during the inspection. The horizontal X-ray beam is positioned to go through the side of an upright product like a can, bottle, or tall carton, optimizing detection performance by reducing the thickness that the X-ray beam travels through.
Food products packaged in tall containers are sensitive to changes in production line speeds and conveyor transfers. The line speeds are often high and the gaps between individual packages are kept at a minimum to achieve high-volume production. This demands more from the production line equipment, including the Critical Control Point.
Ensuring smooth production flow and the rejection of non-conforming products is essential with these packaging types and demands more from the design of the inspection system. That is why SIDEMEKI™ is designed without the need for lead curtains and is equipped with comprehensive product guides to ensure that the food packages transfer effortlessly through the system and inspection.
In the video below, you can see a side-shoot X-ray inspection system (SIDEMEKI™) in action.
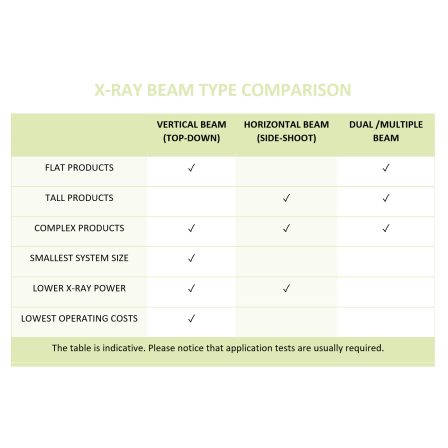
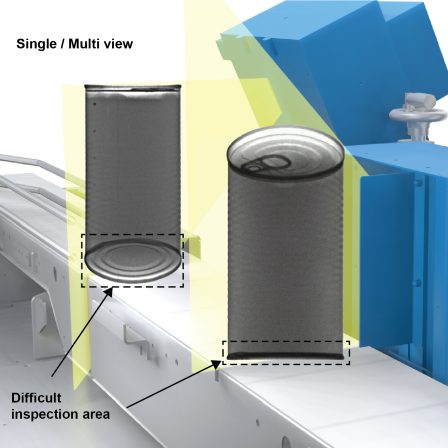
SINGLE BEAM VERSUS DUAL AND MULTIBEAM X-RAY SYSTEMS
When it comes to inspecting tall food products, the detection focus is different compared to other consumer packaged food products. Foreign objects usually end up in the bottom part of the tall food product, and the package quality defects (such as low fill level, open carton flaps, caps, and sealing) are present in the upper part of the tall food product. This challenge of divided focus can be dealt with by having an option for two X-ray generators, to provide the sharpest image for the complete food product.
Products packaged in glass bottles and jars are among the most challenging to inspect, as the base, sidewalls, and neck can cause “blind spots” when inspected with a single X-ray beam. Detecting glass contaminants inside glass packaging, especially thick ones, is a challenging inspection scenario because the packaging and the contaminant have similar densities. The inspection can be improved by using multiple X-ray beams producing images from different angles, reducing blind spots, and optimizing detection to suit specific product types.
For ensuring the best detection results it is recommendable to approach experienced product inspection professionals and usually, individual application testing is also completed.
Application Test Here
Which inspection method to choose?
If you are still unsure which inspection method or solution would fit your operational needs, we are here to help!
Mekitec offers free-of-charge X-ray application testing, where we test your product samples with our primary packaging X-ray inspection systems and provide you a thorough report of the detection rates and overall performance that our systems can deliver.
After reviewing the report, you can make an educated decision on whether X-ray inspection technology would bring additional value to your food quality control.
