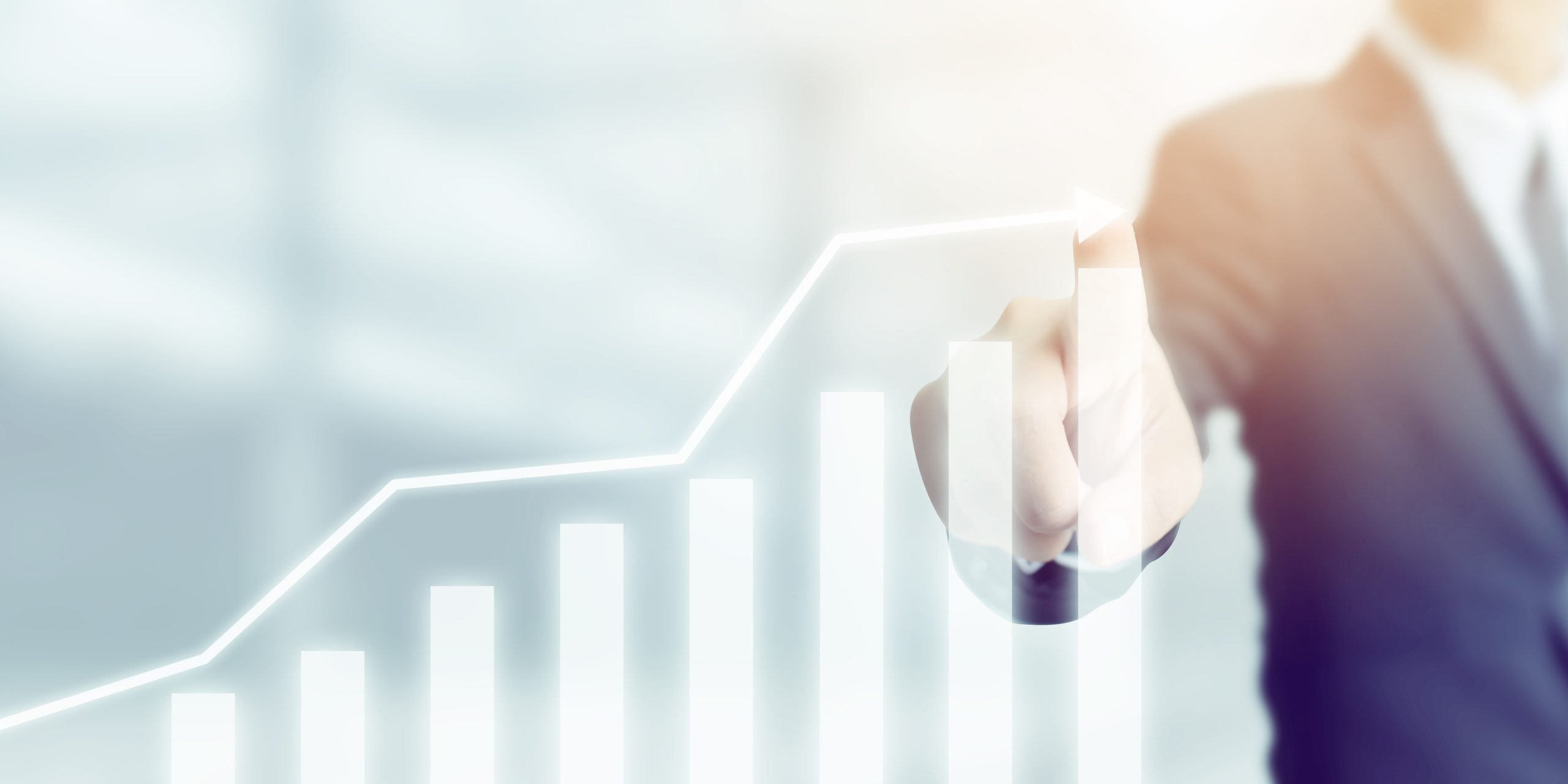
Achieving the full advantage and all of the benefits that come with
X-ray equipment
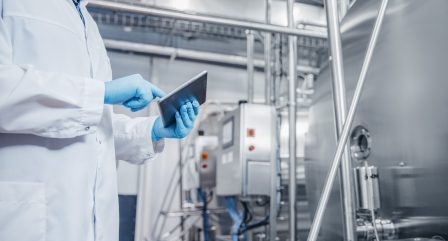
Not just a mandatory investment for food producers
Quality control in food is essential. With X-ray, it is possible to improve the food safety and quality by detecting various quality defects from the production, but the benefits are not limited to food inspection only. Sometimes, using X-ray systems might give a false feeling of security, if the system’s performance is not regularly monitored. In this blog post, we will reveal important aspects in detection equipment management and how this relates to data management which has increasing importance in today’s business and which will be essential to master in the future for every food producer.
This blog is the last part of our 3-part blog series. We recommend reading the previous parts of the series outlining the determination of production needs and the technical characteristics that should be set accordingly before making the decision of the right partner for X-ray solutions to understand the topics discussed in this blog. If you have read the previous parts or are familiar with the themes already, let’s move on to discuss the meaning of “achieving the full advantage and all of the benefits that come with X-ray throughout its lifecycle”.
Find the previous postAchieving the full advantage and all of the benefits that come with X-ray throughout its lifecycle
Reducing expenses and improving quality are often perceived as mutually exclusive since high-value X-ray systems are often associated with higher costs. However, as technology continues to evolve product development has become affordable during recent years. At the same time more sophisticated, complex, and exclusive features are included in the traditional X-ray systems which may have maintained price levels even though these features do not always provide added value to the production. Finding the cost-effective X-ray solution was introduced in the previous blog post. Although the technological characteristics are defined according to specific needs, finding the right solution and achieving full value throughout the lifecycle of an X-ray system can be problematic, as some of the costs incur later during the usage. For example, maintenance costs, prices of the spare parts, and possible human biases can be these kinds of hidden expenses and usually very difficult to predict.
Another problem is that even as the technological improvements have provided many ways to integrate advanced systems and offered cost-reducing solutions to enhance the production capacity, they are no longer serving the needs that food producers are requiring, especially concerning data.
Data management is essential in every organization. To compete in today’s digital era, food manufacturers who can use their data effectively, succeed the best. Even the smallest flaws in the production and its technology can turn into major competitive and financial losses, restricting growth and expansion, and weakening the customer relationships when the company’s data gathering is lacking behind. It is therefore essential to use data to prepare future challenges before they arise and cause damage, and even if they do, the data is used to promptly locate the problem and minimize the consequences.
There are many ways to use data in food production. The gathered data from X-rays consist of X-ray images and production reports of each food production batch, product, and package. When this data is gathered in one location, there are many alternatives available to use and leverage it for various purposes. These are introduced in this blog post.
Data in food production connects to traceability1. Process optimization:
Provide insights into production levels, inventory and capacity availability, and quality levels.
Regular performance tests of the X-ray equipment can detect differences in production capacity. It is also possible to automate a critical control point so that the system alerts when a problem is detected in production, such as an increase in rejects.
For example, if there are two similar production lines equipped with X-ray, comparing the production flows between the lines help identify arising problems. In a case when another line is ineffective (lower capacity or more rejected items compared to another), it might be evidence of failure upstream or X-ray system inefficiencies. Also, unusual changes in production performance, even on a single line, should be investigated further.
Monitoring the production performance helps to accurately manage total production capacity and inventory levels in real-time. X-ray provides a clear indicator that reacts to any changes made upstream, this is extremely valuable when fine-tuning the production equipment to perform better, or when you are introducing new equipment.
Process optimization based on X-ray data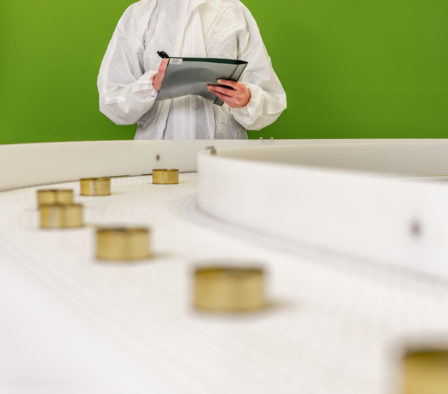
2. Resource consumption reduction:
When the X-ray equipment is located and installed correctly, and there are no operational inefficiencies, it is possible to reduce the amount of false rejects, and foresee and prevent massive product recalls regarding physical contamination in food production.
When the system alerts on contaminated products, it is important to investigate the origin of the quality defect. If the root cause is not investigated, the problem may recur or multiply. However, it is good to keep in mind that in some applications there’s a constant variable risk, for example when the food ingredients are gathered straight from the nature/field.
In production, the detection equipment should only reject non-conforming packages, but sometimes false rejections do happen. There can be multiple reasons why:
- Inadequate sensitivity setup
- Environmental disturbances
- Operational issues
- Incorrect layout/installation
- Detection unit malfunctioning due to internal technical failure
With the help of latest confirmation sensors and data management, food manufacturers can remotely evaluate the data regarding rejected products and identify much easier where, when, and why the rejections occur. The detection performance validation is a crucial part when verifying the critical limits of a control point. This is still done during each production shift/batch by the operators. X-ray systems can help manufactures to provide more visibility into every test made with the system and provide data also remotely to ensure that the system operates in a desired way: to find what is required, and to always remove the products that are deemed to be contaminated. Having the X-ray image enables you to use human eye as well as Artificial Intelligence solutions to fine tune the detection performance to higher standards. There’s a significant value in being able to see what is being detected, why it is triggering on certain parts of the image. Something that was not possible with legacy technologies such as metal detection.
In addition, the collected X-ray images can be used for targeted recalls, if there is an identified risk for contamination in non-rejected products. By investigating the product images of each production batch, it is possible to precisely recall those products which have a foreign object contamination risk before the product reaches the end-customer. This reduces the amount of unnecessary waste since the non-contaminated products are known and saved from the recall.
Reduce waste with X-ray equipment3. Improving customer experiences:
The improved quality and traceability in production turn into a higher customer loyalty and secures the brand reputation.
When the X-ray solution is in use, it is recommended to use gathered X-ray images and create a complete traceability system. If X-ray systems are located in the primary packaging production and the information is available for all of the members in the supply chain, the gathered data can be used for precisely locate food items at all times. If there are many actors in the same supply chain, sharing information is very useful, as it avoids costs from unexpected events and improves relations between the participants. It also facilitates targeted returns and improves customer safety and satisfaction.
Indicating the origin of all food ingredients on a product description/label relays a message that the manufacturer is in control and can be trusted. This is important for both the consumer and reseller. Instead, not knowing such information might give a feeling of lower quality or a possibility for unknown risks, especially if the purchased product has physical hazards. Sometimes this type of information asymmetry may cause a competitive challenge between two similar food brands and the brand which can share such information more openly, becomes the leader.
Read food industry trends 2022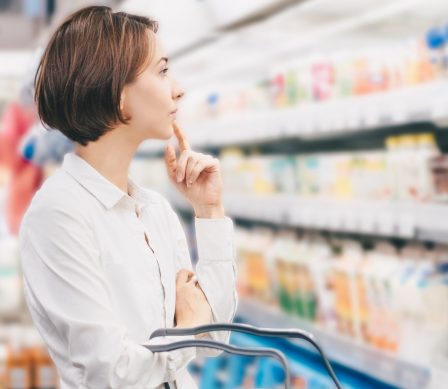
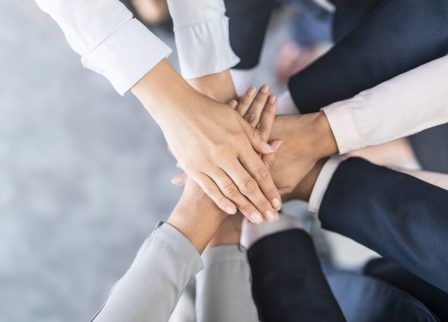
4. Unlock future growth opportunities with your partner:
Reduce unnecessary paperwork and save valuable hours wasted on trying to collect and analyzing data from various incomparable sources, and instead answer all of these needs efficiently now and in the future.
Without proper data and efficient management tools, it is impossible to make reliable decisions and proactively control the food quality while maintaining production efficiency.
It is wise to keep an eye on the X-ray’s lifetime value that emerges from smart data handling. If you find it difficult or time-consuming to analyze data effectively and to maximize the production efficiency and quality by monitoring the data gathered from the X-ray images, you can always ask for help. Your X-ray system provider needs to be a partner for your business and support you alongside the usage of the equipment.
Book a virtual X-ray demo and hear more!Would you like to hear more about traceability and data in food manufacturing?
After reading the blog series, you are now more familiar with the importance of making the right decision of the X-ray equipment, its manufacturer, who is going to be your partner in food quality control, and also the overall management of the equipment to be able to get the full benefit of your investment.
The process begins with need identification by evaluating the nature of the production process. After that, the requirements for the X-ray system are possible to assess. In addition to comparing the X-ray systems and their cost-effective performance capabilities, it is also wise to keep attention to the manufacturer and its after-sales services which might also cause additional expenses during the usage, e.g., when spare parts or remote or local support services are missing, or surprisingly expensive.
Also, be proactive, do not just keep your eyes on the current situation on the markets – the highly competitive food industry requires a forward-looking strategy and the X-ray system provider should anticipate the future challenges for your benefit.
If you would like to know more precisely the traceability and data possibilities, download our e-book!
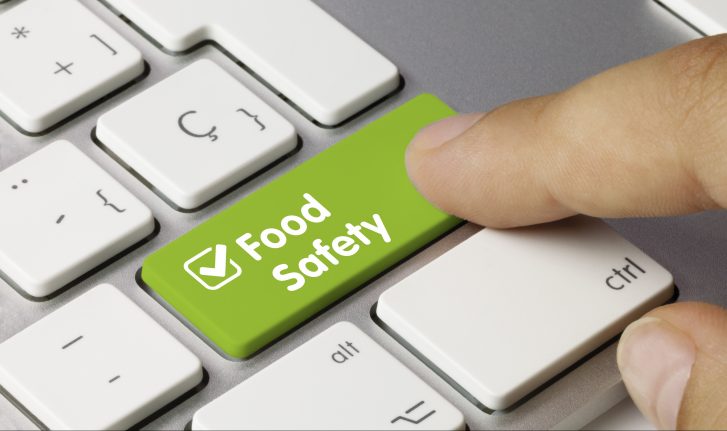