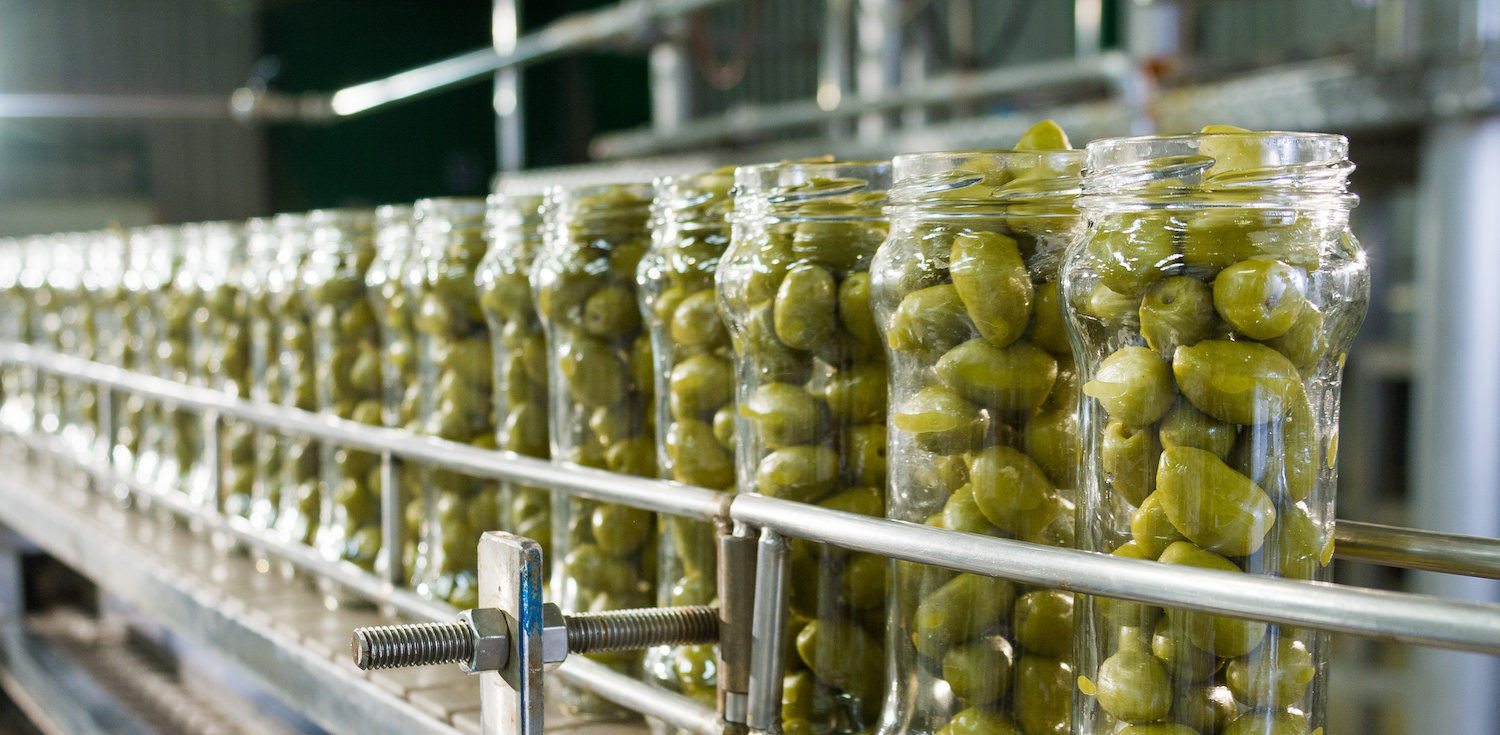
Improving Glass Detection
in Food Production
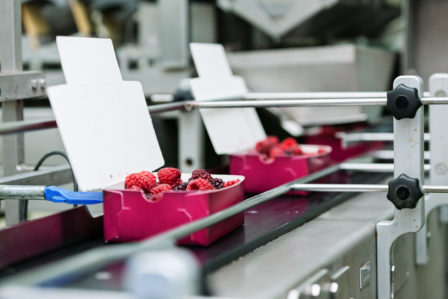
Glass Detection in Food Production
Glass contaminants, such as glass splinters, are highly dangerous contaminants if found in any food production process. If such foreign objects end up in the finished food product, the total damage is massive. The consequences can be e.g. costly recalls if the products have already been shipped out; brand damage caused by bad publicity when food producers need to announce the possibility of contamination and the recall; worst-case scenario being the harm and danger caused to the consumers.
Product recalls due to glass in food
In the past, we have seen several large-scale scandals caused by glass fragments that have ended up in the final packaged food product. The recalls caused by contaminants such as glass can happen regardless of the company size or geographical location.
For example, in 2009 it was reported that several different food products were possibly contaminated with glass in Scandinavia. The fear of contaminated food spread quickly through multiple countries where the products were sold, and a lot of product recalls were made due to the contamination risk.
As a result, the usage of glass materials in food production environments is being minimized all the time. Many large retail chains have their own limitations and regulations for this, but there are still some issues despite these actions. One example is a more recent story from the year 2016 when a global food chain recalled their products because of possible glass contamination in their food production.
DETECTING GLASS IN FOOD WITH X-RAY INSPECTION
When it comes to glass detection in food production, it is obvious that metal detectors lack in technology. That’s why the most suitable solution for detecting glass from your food products is a more superior X-ray technology, that can also detect many other foreign objects in addition to metals and glass.
X-ray inspection is based on the detection of density variations between the actual food product and possible foreign contamination. Glass has a density of about 2,7 g/cm3, but there are multiple different types of glass materials available, such as soda-lime glass (density of 2,54 g/cm3) and crystal glass (density of 3,20 g/cm3).
Since soda-lime glass is the most common form of glass (90% of glass made) and has a low density (i.e. most difficult for an X-ray system to detect), it should also be used when defining the glass detection performance of a certain application.
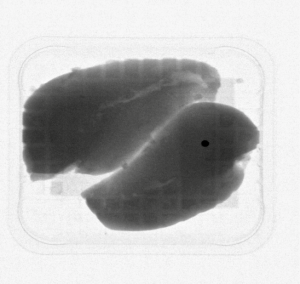
Detecting unwanted glass pieces inside of glass package (e.g. a glass jar or bottle), so-called glass-in-glass detection, can prove to be demanding, and require advanced technology to differentiate the foreign contamination without disturbing the food production.
Sometimes the glass pieces and splinters can be so small and transparent, that they cannot be detected with the human eye or with expensive inspection systems that are based on the vision technology even when the contamination is laying on top of the food product. Obviously, if the contamination is inside of the product, there is no way of detecting it without seeing inside the package. This is where food X-ray inspection proves to be the best solution to automatically detect the small contaminants even inside the packaged food product while the production is running.
GLASS DETECTION WITH MEKITEC X-RAY SOLUTIONS
X-ray systems are indisputably the best solution for glass detection in the food production process. The system can inspect the already packaged food without damaging the final product, therefore being the most efficient inspection method.
Our MEKI X-ray inspection systems are designed to inspect the product in case of any food safety hazards or quality defects. You can find more information about our food safety solutions by clicking the button below.
white paper
More information
By downloading the white paper about primary vs. secondary inspection, you will learn how the inspection of single packaged products brings more value to food manufacturers and guarantees the best food safety and quality assurance.
Fill in the form to gain access to the white paper.
Learn more about our systems
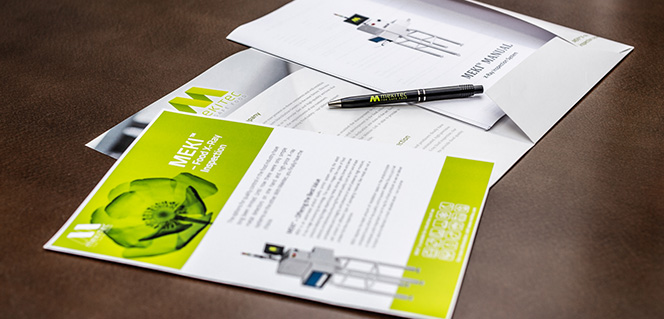